How A Wind Industry Company Is Planning To Solve Its Plastic Waste Problem
- Ishani Karmakar
- 09 March, 2023
- 2 mins ago
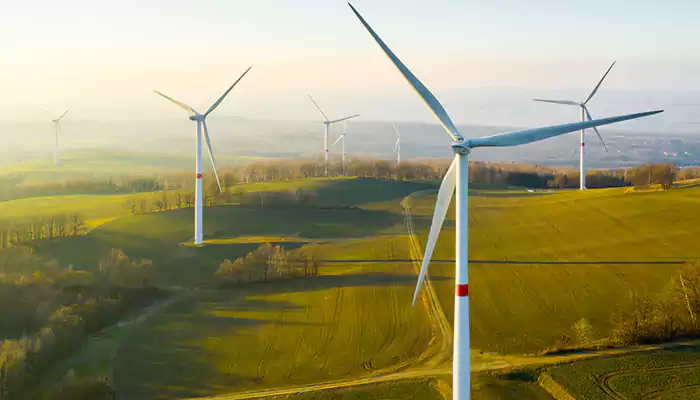
How A Wind Industry Company Is Planning To Solve Its Plastic Waste Problem
One of the world's largest producers of wind turbines claims to have a game-changing answer to the problem of excessive plastic waste in the sector.
Vestas has publicised an innovative method for recycling the plastic used in turbine blades into new raw materials. It may then be reused to create new turbines rather than filling up landfills.
Here's why that's a really massive undertaking. Blades on today's turbines are longer than the Statue of Liberty, and they are gradually engulfing both land and water. They're made to last for decades in the worst conditions and are exceptionally strong. But, after they have lost their usefulness in society, they are often discarded. By 2050, it is estimated that there will be 43.4 million tonnes of turbine blades in landfills throughout the world.
A huge impact Little details about Vestas's new method for recycling the plastic in turbine blades have been shared till date. There are significant obstacles to be overcome, but if the firm succeeds, it might revolutionise the wind industry.
Indications are that it has the potential to be really significant. To begin, regular plastic is not used in the construction of the turbine blades. Epoxy is like super practical plastic, and Vestas claims to have found a method to recycle it. It has been chemically modified to be extremely durable. That's why it's suitable for use in spacecraft, aircraft, and wind turbine components due to its extreme durability.
The vast majority of the plastic we come into contact with on a daily basis is pliable enough to be melted and reshaped. The epoxy is unique. The material is a thermoset plastic. When cured, the molecules in its chains form very strong connections, or crosslinks, that are virtually impossible to break. Because of this, epoxy will maintain its chemical structure and form even when subjected to high temperatures.
A revolutionary product Vestas, in conjunction with Aarhus University, the Danish Technological Institute, and Olin, an epoxy producer, uncovered the crucial chemical process. The blade is immersed in a solvent that will dissolve the epoxy and allow the other components, often glass or carbon fibres, to float to the surface. The second stage involves further treatment of the epoxy to further break it completely down into its chemical elements.
The procedure has only been successfully demonstrated on a limited scale utilising "parts of turbine blades" by the business so far. There are still many major issues to solve. Vestas has said that they can recover a major portion of the epoxy from used blades using their procedure, although they have not provided a specific percentage as of yet.