Understanding Temperature Gauges – How They Measure Up
Temperature gauges are indispensable instruments in a wide range of industries, from manufacturing to food processing, and even in residential settings.
- Ishani Karmakar
- 18 March, 2024
- 2 mins ago
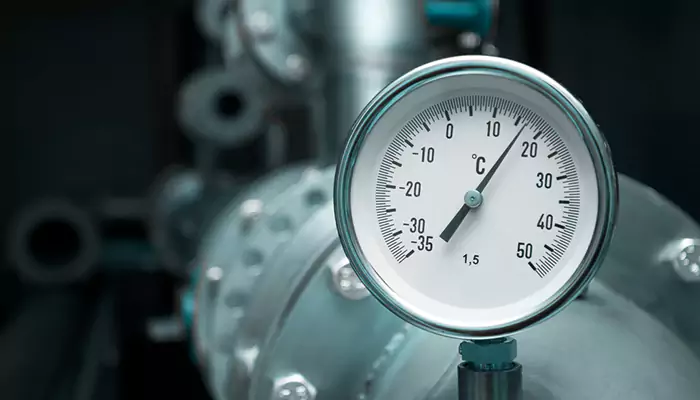
Understanding Temperature Gauges – How They Measure Up
Temperature gauges are indispensable instruments in a wide range of industries, from manufacturing to food processing, and even in residential settings.
These devices provide critical information about the temperature of a substance or environment, enabling precise control over processes, safety measures, and comfort levels. Understanding how temperature gauges work, their types, applications, and limitations can provide valuable insights into their essential role in our daily lives and industries.
The Science Behind Temperature Measurement
Temperature measurement is grounded in the principles of thermodynamics, the branch of physics that deals with heat, temperature, and their relation to energy and work. A temperature gauge measures the thermal state of a substance or environment, often converting the physical property changes of materials under temperature variations into readable data. The accuracy and reliability of a temperature gauge depend on its design, the measurement principle it employs, and the calibration process it undergoes.
Types of Temperature Gauges
There are several types of temperature gauges, each suited to particular applications and measurement ranges. The most common include:
Mercury and Alcohol Thermometers: Utilizing the physical expansion of liquids under heat, these traditional thermometers are simple but limited by their fragility and the toxicity of mercury.
Bimetallic Thermometers: These devices measure temperature through the differential expansion of two metals bonded together. They are robust and suitable for a wide range of industrial applications.
Thermocouples: Perhaps the most widely used type in industrial settings, thermocouples work on the principle of the Seebeck effect, where a voltage is generated at a junction of two different metals that is proportional to temperature.
Resistance Temperature Detectors (RTDs) and Thermistors: Both of these sensors measure temperature by the change in electrical resistance of a material with temperature. RTDs are known for their precision and stability, while thermistors offer a high degree of sensitivity.
Infrared Thermometers: These non-contact devices measure the infrared radiation emitted by an object, allowing for temperature measurement from a distance, which is ideal for moving or hazardous objects.
Applications Across Industries
Temperature gauges find applications in nearly every sector:
Manufacturing: Ensuring materials are processed at the correct temperatures to maintain quality and safety.
Food and Beverage: Monitoring storage, cooking, and refrigeration temperatures to comply with health standards.
Healthcare: Ensuring the correct storage temperatures for medications and samples, and monitoring patient body temperatures.
HVAC: Controlling ambient conditions within buildings for comfort and energy efficiency.
Automotive: Monitoring engine and exhaust system temperatures to ensure performance and safety.
Calibration and Maintenance
The accuracy of temperature gauges is paramount; thus, regular calibration is necessary. Calibration involves comparing the readings from a gauge to a known temperature standard and making adjustments as necessary. Maintenance practices also play a crucial role in ensuring the longevity and reliability of these instruments. This includes regular inspections, cleaning, and replacement of damaged parts.
Limitations and Considerations
While temperature gauges are versatile and essential, they are not without limitations. Measurement errors can occur due to improper calibration, sensor degradation over time, or incorrect application. Environmental factors, such as electromagnetic interference for electronic sensors, can also affect readings. Selecting the appropriate type of temperature gauge for the specific conditions and application is critical to obtaining accurate measurements.
Advances in Temperature Measurement Technology
Technological advancements have led to the development of smarter, more resilient temperature gauges. Innovations include wireless sensors for remote monitoring, devices with digital outputs for direct integration with control systems, and materials that can withstand extreme conditions, from cryogenic temperatures to the interiors of combustion engines. Furthermore, the integration of AI and machine learning algorithms enables predictive maintenance by analyzing temperature data trends to anticipate failures before they occur.
Temperature gauges play a critical role in a myriad of applications, providing the necessary data to maintain quality, efficiency, and safety in processes across industries. Understanding the types of temperature gauges, their applications, and the science behind them enables better selection, use, and maintenance of these essential instruments.